Expert Recommendations on What is Porosity in Welding and How to Resolve It
Wiki Article
Porosity in Welding: Identifying Common Issues and Implementing Finest Practices for Prevention
Porosity in welding is a prevalent issue that frequently goes undetected until it creates significant issues with the integrity of welds. This common flaw can compromise the strength and resilience of bonded structures, posturing safety and security threats and causing expensive rework. By comprehending the origin of porosity and implementing effective prevention approaches, welders can significantly boost the top quality and dependability of their welds. In this discussion, we will discover the crucial elements contributing to porosity formation, examine its damaging results on weld performance, and review the very best techniques that can be taken on to decrease porosity occurrence in welding procedures.Typical Sources Of Porosity

Making use of filthy or damp filler materials can introduce contaminations into the weld, contributing to porosity concerns. To reduce these usual causes of porosity, complete cleansing of base steels, correct protecting gas choice, and adherence to optimum welding specifications are important techniques in achieving top quality, porosity-free welds.
Influence of Porosity on Weld Quality

The presence of porosity in welding can significantly jeopardize the structural stability and mechanical homes of welded joints. Porosity develops spaces within the weld steel, damaging its overall strength and load-bearing capacity. These voids serve as tension concentration factors, making the weld a lot more susceptible to breaking and failing under applied tons. Additionally, porosity can decrease the weld's resistance to corrosion and various other environmental factors, even more decreasing its long life and performance.
Among the primary consequences of porosity is a decrease in the weld's ductility and durability. Welds with high porosity degrees tend to exhibit reduced influence stamina and decreased ability to deform plastically prior to fracturing. This can be especially concerning in applications where the welded components undergo dynamic or cyclic loading conditions. Porosity can hinder the weld's capacity to effectively send pressures, leading to premature weld failure and potential security hazards in critical frameworks. What is Porosity.
Best Practices for Porosity Prevention
To enhance the architectural integrity and high quality of bonded joints, what particular steps can be executed to decrease the incident of porosity during the welding process? Making use of the proper welding technique for the specific material being welded, such as readjusting the welding angle and gun placement, can further prevent porosity. Normal assessment of welds and instant remediation of any kind of issues recognized throughout the welding process are necessary methods visit here to stop porosity and create high-quality welds.Relevance of Appropriate Welding Methods
Applying proper welding methods is vital in ensuring the structural integrity and quality of bonded joints, building on the have a peek at this site structure of efficient porosity avoidance actions. Welding methods directly affect the total strength and sturdiness of the bonded structure. One vital facet of appropriate welding techniques is preserving the proper warmth input. Excessive warmth can result in raised porosity as a result of the entrapment of gases in the weld pool. Conversely, not enough warm might cause incomplete combination, developing prospective powerlessness in the joint. In addition, using the appropriate welding specifications, such as voltage, existing, and take a trip speed, is important for attaining sound welds with minimal porosity.In addition, the choice of welding procedure, whether it be MIG, TIG, or stick welding, must straighten with the details demands of the task to make sure optimal results. Appropriate cleansing and prep work of the base steel, as well as choosing the ideal filler material, are additionally necessary parts of skilled welding strategies. By adhering to these best techniques, welders can lessen the danger of porosity development and create high-grade, structurally sound welds.
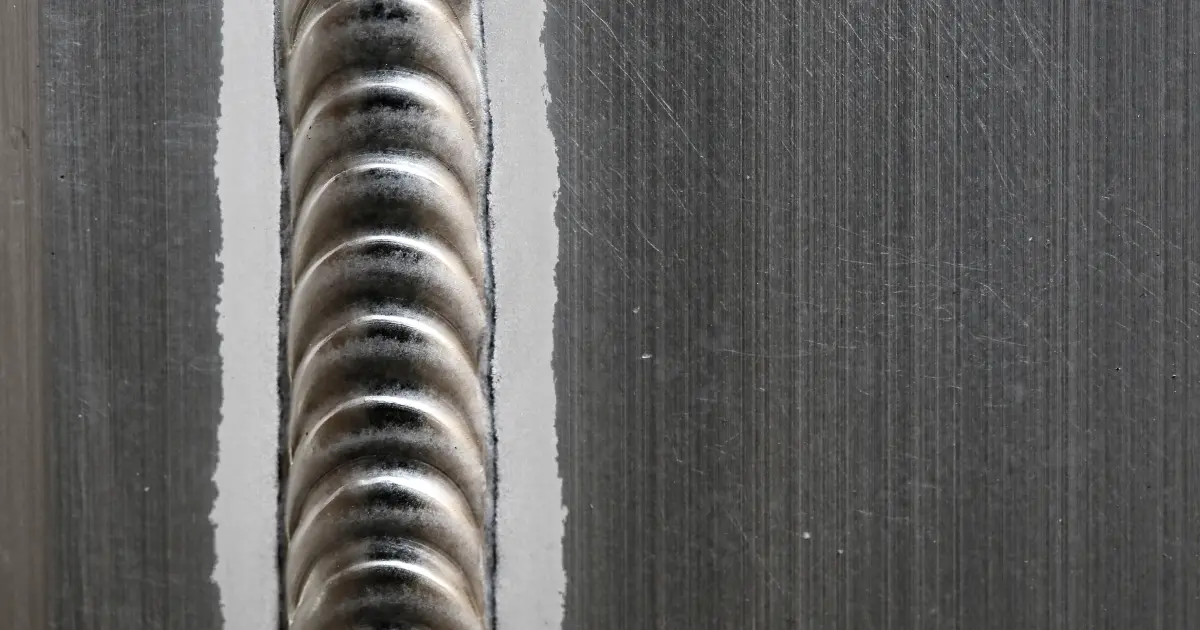
Checking and Quality Control Steps
Quality control measures play a critical role in verifying the integrity and dependability of welded joints. Checking procedures are essential to spot and avoid porosity in welding, guaranteeing the stamina and resilience of the end product. Non-destructive testing methods such as ultrasonic testing, radiographic screening, and visual examination are frequently used to identify potential defects like porosity. These techniques enable for the assessment of weld top quality without endangering the honesty of the joint. What is Porosity.Post-weld inspections, on the other hand, analyze the last weld for any Homepage problems, including porosity, and verify that it fulfills defined requirements. Executing a detailed quality control strategy that consists of extensive testing procedures and evaluations is extremely important to lowering porosity concerns and ensuring the general top quality of welded joints.
Conclusion
To conclude, porosity in welding can be an usual concern that impacts the high quality of welds. By identifying the usual reasons of porosity and carrying out best methods for prevention, such as appropriate welding strategies and screening measures, welders can make certain high quality and dependable welds. It is important to focus on prevention techniques to decrease the occurrence of porosity and maintain the honesty of welded structures.Report this wiki page